Webinar
Understanding the Benefits of BFS Unidose for Ophthalmics as an Alternative to Glass Vials
On-demand

Blow-fill-seal (BFS) technology is fast rising to the top of the agenda as a promising container format for pharmaceutical and biotech companies developing sterile ophthalmic therapies.
This efficient manufacturing process sees plastic containers blow-formed, filled and sealed in a sterile environment. They are ideal for offering single doses of sterile drug products — not just ophthalmics, but also injectables and inhalation treatments — enhancing self-administration convenience while reducing the risk of product waste.
BFS unidose format offers unique benefits including:
- No need for preservatives in unidose and less risk of microbial contamination as the container is sealed as soon as it is filled with formulation and contains only a single dose
- Minimised risk of breakage, as it is made of plastic, not glass, reducing the need for secondary packaging, and cutting transport and storage costs
- Production advantages using plastic instead of glass vials due to a lower risk of component supply shortages and it provides a faster, simpler, and cheaper process, and also has a lesser environmental impact
BFS is suitable for solutions, gels, suspensions and emulsions, and for even the most sensitive treatments, such as biologics, supporting stability through the use of temperature-controlled storage or nitrogen atmosphere filling.
But how can pharma and biotechs effectively harness BFS technology? What should companies bear in mind?
In this webinar, we will explore the numerous advantages BFS unidose format offer over multidose options for ocular applications, as well as over single-dose glass vials. We will dive into the aspects companies need to consider to utilise BFS in ophthalmic drug development and outline how Recipharm can support making the most of this technology.
Webinar Learning Objectives:
- What is BFS technology and the unique benefits of unidose BFS for ophthalmics, biologics and other sterile drug products
- What are the advatanges of BFS unidose format in comparison to ocular multidose or glass vial format?
- How Recipharm can support companies in switching to unidose BFS
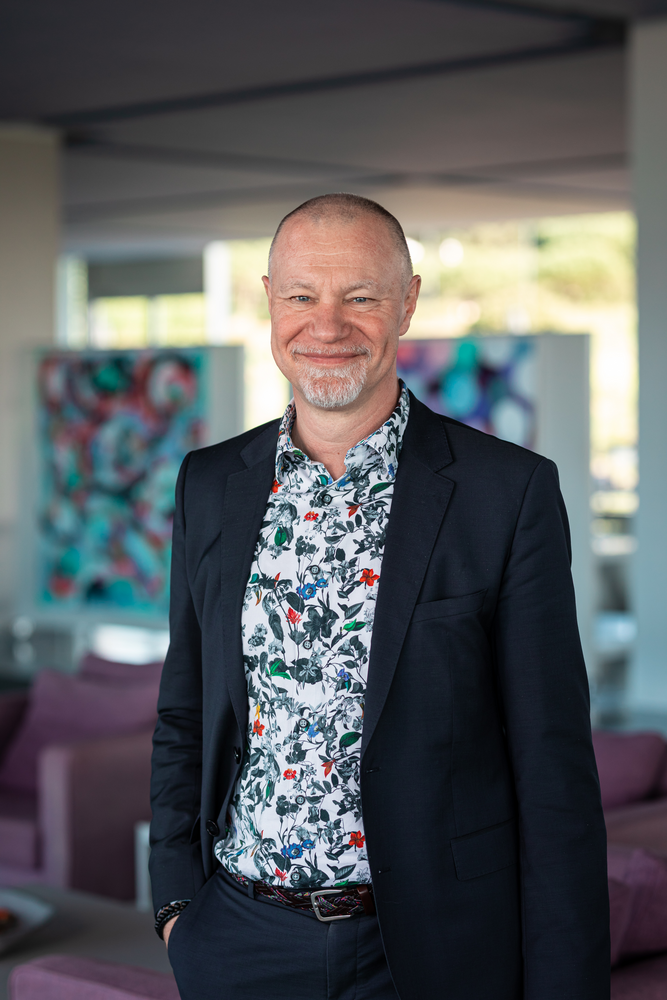
Yves Buelens
Yves Buelens is an industrial pharmacist with 30 years’ experience in the pharmaceutical industry, working with various technologies (sterile and non-sterile).
Yves previously worked with several big pharma companies (Upjohn, Schering-Plough, J&J, Alcon/Novartis) and CDMOs (Nextpharma, Catalent) environment. His responsibilities increased over time, in various departments, among which are production, maintenance, engineering, QA (including a QP position) and sales.
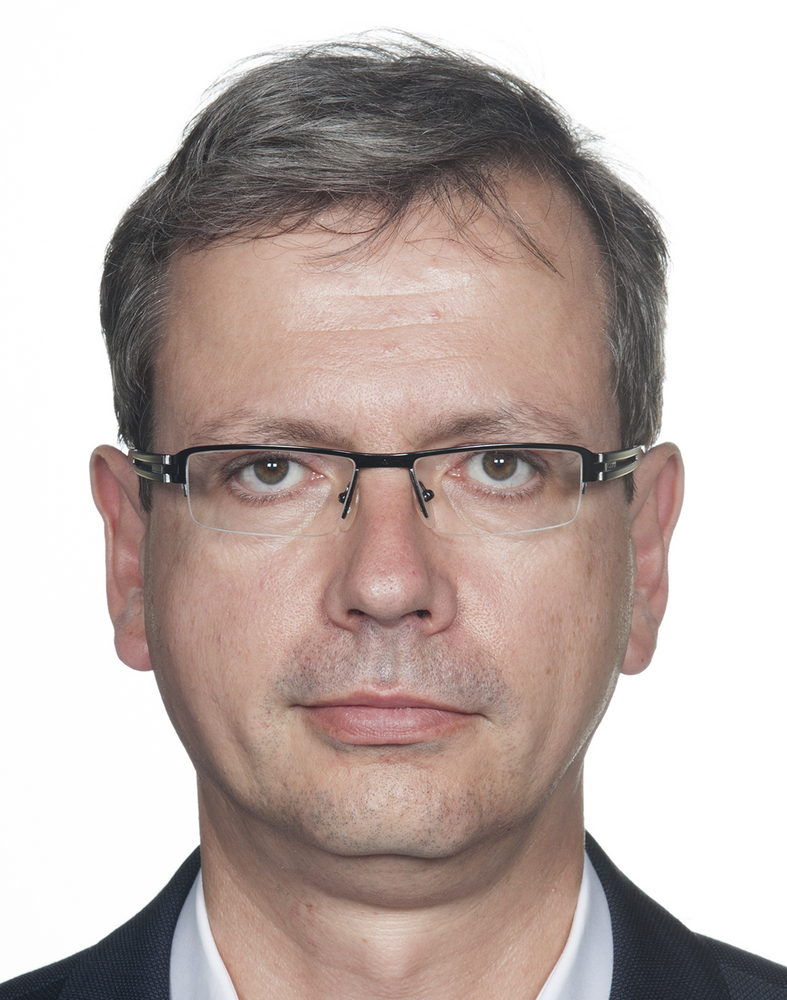
Jean-Christophe Moreau
As Technical Transfer Director at Recipharm, Kaysersberg site (France), Jean-Christophe Moreau leads the team responsible for introducing new BFS products on site.
He is a pharmacist with 29 years’ experience within the pharma industry across several companies, technologies (sterile and non-sterile), positions and countries – mainly in the field of quality, production and CDMO management. Jean-Christophe previously worked with Novartis in Switzerland as Supplier Relationship Manager, with Delpharm in France as Plant Manager, with Boehringer Ingelheim in France and Germany as QC head and Production Director and VP Pharma Production then Senior Manager Third Party Network - Asia and Europe, respectively.
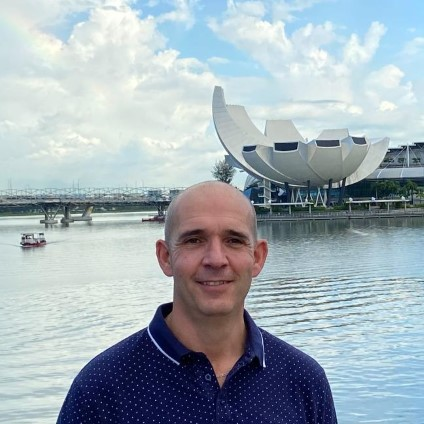
Christophe Schwoehrer
Christophe Schwoehrer is a manufacturing science and technology aseptic filling expert at the Recipharm Kaysersberg (France) site. In 2022, he gained the role of Chairman of the Pharmaceutical Blow-Fill-Seal International Operators Association (BFDS IOA).
Christophe has 32 years’ experience in maintenance and project management within the pharma industry and currently manages early R&D products design and production on LAB+ small-scale machines on site.